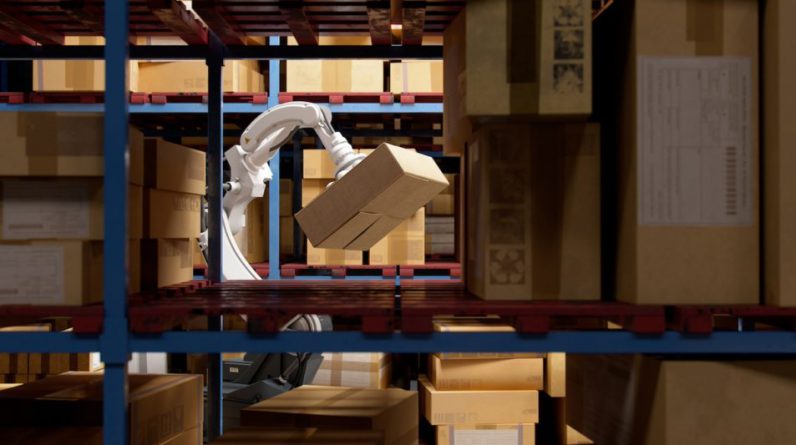
Automation in the warehouse catapults productivity to new heights and can significantly decrease labor and operational costs. These benefits help to explain why experts predict that 26% of warehouses will have some form of automation installed by 2027.
However, deploying automated or AI-based robotic systems in a warehouse is no easy feat, especially considering that most warehouses are built for human workers. A few warehouse robots are bipedal, but most differ from humans in substantial ways, such as footprint (size) and movement capability. As a result, it can be challenging to retrofit a space optimized for humans.
Additionally, it’s essential to consider the change management process your human workers should expect as you deploy robots into the warehouse. Stakeholders off the warehouse floor should also fully understand the benefits of warehouse automation — before deployment, not after.
Let’s review a few other best practices as you consider adopting automation.
Achieve buy-in. Before drafting workflows or contacting an automation provider, leaders should work to achieve buy-in from those most impacted by adoption: warehouse operators and frontline workers. Leaders should understand and address employees’ apprehensions about automation (if any).
For instance, some employees may fear for their job security. If that’s the case, explaining your long-term labor plan for the warehouse may be helpful. Perhaps you plan to upskill current workers so they can provide guidance to AI-based automation systems, creating a human-in-the-loop ecosystem. Or you may not intend to alter your current labor structure at all. Communicating this expectation is critical to ensure everyone is on the same page.
By engaging with your employees before adopting automation, you’ll gain valuable insights into potential pain points and stumbling blocks. Identifying these potential challenges early can simplify the change management process in the long run. Furthermore, you can take this opportunity to educate your employees about the benefits of automation, which may include reduced physical labor and safer working conditions.
Engage stakeholders early and often. Communication doesn’t end with your employees. Everyone whose lives will be affected by automation should be apprised of all plans before they unfold. Possible stakeholders include C-suite executives, board members, operations managers and IT teams.
Level-setting is critical at the outset of adoption, because some stakeholders may have an inaccurate understanding of warehouse automation or the timeline associated with its adoption. Addressing these misconceptions can improve the sentiment toward automation and boost the likelihood of success.
That, of course, prompts the question: What constitutes “success”? Gather feedback from all stakeholders to answer this question. Ultimately, you should have enough information to develop KPIs and other metrics for success. These might include metrics related to increased throughput, or decreased labor turnover.
Consider all ramifications and roadblocks. Exceptions on the warehouse floor are common because very few packages or parcels are identical, yet they can be tricky to notice. Still, it’s helpful to assess your current workflow for potential automation hiccups. For example, do your human workers routinely smooth labels to help with scanning? This small and seemingly inconsequential step might prove challenging for certain systems to accomplish or “learn.”
These issues can usually be addressed by adopting AI vision systems that accept human feedback. But automation systems operating without a human for guidance — or those without AI — may struggle to handle small but significant workflow changes. It’s best to identify these potential roadblocks before adoption.
Train before you deploy. For best results, consider implementing a training feedback loop. In practice, this might look like:
1. Identifying your team: Who will be working with automated systems in a daily, hands-on capacity? These individuals will be the most important to train and gather feedback from.
2. Building your processes: Develop comprehensive training programs and formal documentation with your automation provider. These documents should cover standard operating procedures as well as troubleshooting and maintenance guidelines.
3. Gathering feedback: Once you’ve built these processes, run them by your team. What issues do your workers foresee?
4. Reiterating: Use feedback to rebuild your proposed processes. Then, gather input and repeat until all workers agree on the SOPs and feel confident about automation deployment.
5. Installing: Only once all on-the-ground stakeholders agree about your processes should you deploy automation.
Determine your troubleshooting process. Following the steps outlined in this article will greatly improve your odds of a successful automation rollout. However, issues are bound to arise. That’s why it’s important to determine your troubleshooting procedures.As such, ensure all relevant contact information, escalation procedures and troubleshooting information are well-documented and readily accessible to your staff. Regularly review and update this information with your provider to ensure it remains correct. Once deployment has started, it’s a good idea to periodically test your staff’s knowledge of troubleshooting procedures. These drills help improve the likelihood of quick mobilization in the event of actual system failure.
Train, train, train. The first five steps, above, are pivotal for easing the adoption process at the outset. This final step is crucial for long-term success. Remember that no system or warehouse is perfect, and continuous improvement is the most effective way to ensure your operating procedures remain competitive — especially in such a turbulent industry.
Discuss with your automation provider how to continuously train your staff and upgrade your AI systems to keep pace with the competition. Host regular, interactive training sessions with your staff, and continue to communicate the benefits of automation.
Although not comprehensive, this roadmap is a great place for leaders to start as they assess how to deploy automation in their warehouses. Remember, the key to success lies in a worker-first approach to automation. After all, people remain this industry’s greatest asset.
Christina Gomez-Terry is the VP of Operations at Plus One Robotics.