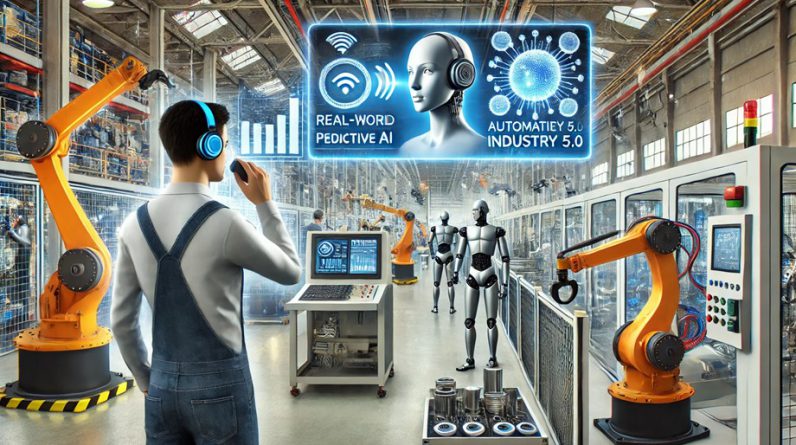
The evolution of industrial automation has brought us to Industry 5.0, a paradigm shift that prioritizes human-centric manufacturing, integrating artificial intelligence (AI) and human collaboration for enhanced decision-making and efficiency. The role of augmented intelligence – a hybrid model where AI assists human operators rather than replacing them – has become increasingly vital. One of the most promising advancements in this domain is the integration of voice assistance technology with Automated Machine Learning (AutoML), allowing human workers to interact seamlessly with AI-powered decision support systems in real time.
A recent study, “Augmented Intelligence with Voice Assistance and Automated Machine Learning in Industry 5.0” by Alexandros Bousdekis, Mina Foosherian, Mattheos Fikardos, Stefan Wellsandt, Katerina Lepenioti, Enrica Bosani, Gregoris Mentzas, and Klaus-Dieter Thoben, published in Frontiers in Artificial Intelligence, explores how voice assistants combined with AutoML can enhance manufacturing processes. This study proposes a human-machine collaboration framework, where factory operators leverage voice-enabled AI systems to access data-driven insights instantly, streamlining industrial operations.
The role of augmented intelligence in Industry 5.0
Industry 5.0 builds on the automation and efficiency of Industry 4.0 but emphasizes human well-being, enhancing the synergy between human intelligence and AI-driven automation. Traditional AI-based automation often removes human intervention, but augmented intelligence seeks to empower human operators by providing real-time insights through conversational AI interfaces. Voice-enabled digital intelligent assistants (DIAs) act as intermediaries between human workers and AI systems, offering a natural and intuitive means of interaction.
One of the main challenges in modern manufacturing is the complexity of data processing and decision-making. AutoML simplifies this by automating the creation, selection, and optimization of machine learning models, allowing even non-experts to benefit from AI-powered insights. By integrating voice assistance with AutoML, the study presents a practical and scalable solution for real-world manufacturing environments, reducing cognitive load, minimizing errors, and enhancing productivity.
Integrating voice assistants with AutoML: A smart manufacturing approach
The researchers propose a three-layered architecture for integrating voice assistants with AutoML in a real-world manufacturing environment:
- Voice Assistant Module: This layer provides a natural interface for users through Speech-to-Text (STT) and Text-to-Speech (TTS) technologies, allowing operators to query AI models in natural language.
- Analytics Service Module: This component automates the construction of ML models using AutoML frameworks, enabling data processing and predictive insights in real-time.
- Use Case Infrastructure: The final layer integrates the AI system with existing manufacturing databases, production systems, and quality control mechanisms.
Through this architecture, human operators can ask questions, request insights, and interact with machine learning models through voice commands. The AutoML framework processes large datasets in the background, delivering actionable recommendations without requiring deep AI expertise from the user.
Real-world implementation: Enhancing quality control in manufacturing
To validate their approach, the researchers deployed their system in a real-life manufacturing environment – specifically, in the quality control operations of Whirlpool, a leading home appliance manufacturer. The study focused on improving end-of-line quality testing using AI-driven insights.
Operators in the Whirlpool factory used the voice-enabled assistant to access predictive maintenance alerts, defect classification, and statistical process control insights. The system enabled workers to receive automated recommendations on defective products, categorize faults, and optimize inspection processes. The AutoML-driven analytics allowed real-time defect prediction, significantly improving fault detection accuracy and reducing response times.
The implementation demonstrated that:
- Voice assistants improved efficiency, allowing operators to query AI systems hands-free.
- AutoML reduced the need for expert data scientists, making AI accessible to factory workers.
- Predictive analytics enhanced decision-making, enabling proactive responses to manufacturing defects.
Evaluation and future prospects
The researchers conducted an extensive evaluation to measure the system’s impact on AI trustworthiness, usability, cognitive workload, and technical robustness. Using the Assessment List for Trustworthy Artificial Intelligence (ALTAI), the study found that the system excelled in privacy, transparency, and accountability but required further refinements in human oversight and adaptability.
Users reported high satisfaction with the voice interface, particularly its ability to simplify complex analytics through natural language processing. However, challenges such as voice recognition accuracy in noisy environments and ensuring high-quality training data for AutoML models remain areas for improvement.
Moving forward, the research suggests enhancing explainability in AutoML, improving multi-user support for DIAs, and integrating wearable interfaces like AR-assisted smart glasses. As Industry 5.0 progresses, AI-powered voice assistants will play an essential role in creating human-centric, intelligent manufacturing environments, ensuring that AI enhances – not replaces – human expertise.
Conclusion
This study marks a significant step toward seamless human-AI collaboration in Industry 5.0. By combining voice assistants and AutoML, manufacturers can bridge the gap between AI-powered decision-making and human intuition, leading to smarter, safer, and more efficient production lines. As industries continue to adopt augmented intelligence, this hybrid approach will redefine the future of manufacturing, ensuring that technology enhances productivity while keeping humans at the center of the process.