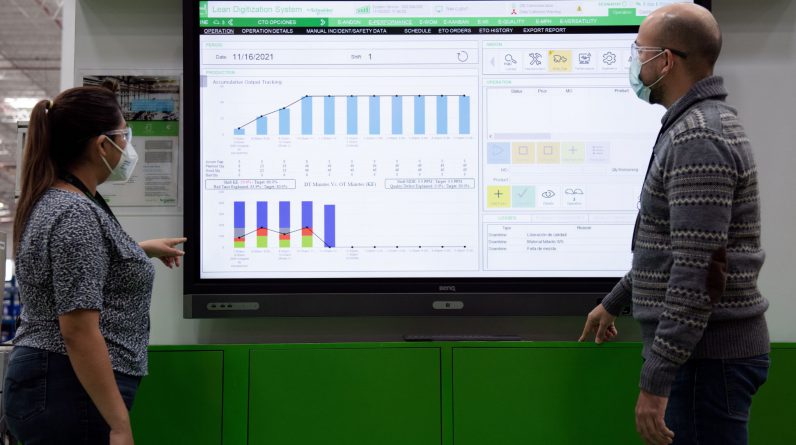
As artificial intelligence (AI) starts to take root across industries, plenty of people are probably wondering: Are the machines coming to take our jobs?
Depending on who you ask, the answer is mostly “no,” but also “yes.”
Hany Fouda, the senior vice president of Schneider Electric Process Automation, is responsible for developing and executing technology and commercial strategies. He leads diverse, specialized, global teams that enable game-changing technologies, develop a wide range of power and process projects, and leverage a broad spectrum of automation products, systems, services, and industrial software.
Right now, all of that stuff seems to funnel back into a conversation about AI. I caught up with Fouda at CERAWeek by S&P Global in Houston, Texas, and asked how he envisions AI impacting the renewable energy and transmission and distribution (T&D) spaces. We touched on a wide range of topics, including supply chains and the modern workforce. Below, you’ll find a transcript of our discussion that has been shortened and touched up for clarity and conciseness.
Paul: Let’s start with a little bit about AI. I feel like that’s a hot topic of conversation for so many folks right now- how we integrate it with our workforce, and how we make it work for us. What are your thoughts, holistically, on AI- and how are you implementing it at Schneider Electric?
Hany Fouda, SVP of Schneider Electric Process Automation
Hany: So, we recognize that AI will be a transformative technology for us, and at Schneider, we decided early on to create an AI hub within the organization. We really look for ways or use cases for AI to be deployed within Schneider Electric itself, especially in our factories. We own 200 factories across the globe (40 in the United States), so we can deploy our technology with our operators in a typical environment. These factories are humming 24/7, and we constantly test our technology.
So we look into ways to use AI to improve our factory operation, reduce energy consumption, reduce waste, reduce water usage, and build up more efficiency and productivity across the workforce. We have started infusing this technology with the existing workforce; one of our factories, for example, is a multi-generation factory. So the younger generation is working with those who have been running the plant for 30 or 40 years, and they’re both using the AI technology. For AI to be effective and certainly scalable, the workforce has to buy in. The new generation, as well as those who have been operating the plant for many years, have to see a value. What’s in it for them? The operators that have been running the plant for quite some time now have more free time to do better things that they love to do rather than the mundane stuff that the AI can be utilizing.
From my perspective, AI is just a tool, like any other tool, any other technology that we develop. Yes, there is a lot of hype, because it’s highly accelerated, but it’s the same as we have done with the Internet or the personal computer. It takes a while. Maybe the timespan for this adoption is shorter than other technologies because it’s happening in a more condensed way, and it is also driven by national defense, cyber security, and so on… But at the end of the day, it is about people leveraging technology to improve their productivity and improve how they produce the outcomes that they need.
Access to power has become the key driver of AI and data center growth, prompting the need for new solutions among utilities, developers, and other stakeholders. This demand growth will test grid reliability, requiring new ways of collaboration and policy structures.
A new DISTRIBUTECH event, DTECH Data Centers & AI, will help stakeholders in this burgeoning industry navigate power constraints and project delays while balancing the demand for sustainable, flexible solutions. Influential executives and thought leaders will assemble in San José, California from May 27-29, 2025 to discuss how AI is transforming the utility landscape and explore ways power providers can manage increasing demand while utilizing the revolutionary tools promised by new technologies.
Registration for DTECH Data Centers & AI is now open – secure your spot today!
Paul: AI can be a bit of a double-edged sword because it’s such a power suck. How do you balance a dire need for more generation with what AI could do for the energy industry, at the manufacturing scale and all the way down the value chain?
Hany: You’re absolutely right. Today, to train a model, you need a lot of energy, and this energy is money, basically. I think ChatGPT-4 consumed roughly $100 million to get trained. I think the next one will be $1 billion, and the next one will be $10 billion, right? But that doesn’t mean that it has to continue to be exponential this way.
There are many ways that Schneider Electric is working to redesign data centers to be more efficient. We’re working with NVIDIA and others to provide the cooling, for example. These data centers train the models themselves, but when you prompt an AI to look for something, it’s really costing energy because it has to go and find what you’re looking for in the model itself. So what we’re working on is improving the efficiency of the data center itself, working with the chip manufacturers because they are improving their efficiency in terms of chip design as well. A new generation of chipsets is actually allowing us to figure out a way to reduce the energy consumption and the cooling requirement on the chip as well as helping us to budget our energy consumption as we move forward with the various models. And that’s the core of what Schneider Electric is trying to do. We are an energy efficiency company, and we live and die with our customers in terms of saving them energy consumption.
Paul: Efficiency, I imagine, gets complicated when supply chains get snagged. Here in the US, for example, there is a rush to onshore domestic manufacturing to simplify supply chains and avoid tariffs. How have supply chain and tangential issues complicated your work, and how have you found ways around those snags?
Hany: I would say the complications started with COVID, right? It was obviously a health issue that we faced collectively as human beings, and we had to figure out a way to manage our supply chain under restrictions because of the shutdown in many countries. And that lesson, actually, helped us a lot to redesign our supply chain to look for resiliency and robustness.
We created programs like “the power of two,” where we are looking into ways to de-risk our supply chain by manufacturing in the United States and also manufacturing in Europe for the same product. So if anything happened in one manufacturing facility, either in the US or Mexico, then we have alternative supply coming in.
We also work with our suppliers to improve their resiliency as well, so that we are not so much dependent on one location or one factory in our supply chain. Now, disruptions happen. Some things are out of our control, but how we respond to it is part of what we do at Schneider Electric. For example, we created a control tower that is constantly looking into our flow of supply. It’s very common that a single product can cross borders between countries many times, you see that in the automotive industry as well, and how we can drive resiliency in that cycle is a critical piece of what this control tower is always looking for.
Paul: I think all of this eventually funnels back into workforce stuff, whether it’s having manufacturing redundancies or implementing AI, you still have to have the people to pull it off. What are some of the workforce challenges you’re facing, and how does the arrival of AI technology both hurt and help?
Hany: I think that the workforce has always been a race for talent, and one of the impediments to deploying AI at scale in many companies is the lack of AI-trained people who really understand how to manage it as you scale up. You can do a proof of concept, but the question is: do you have the right workforce to help you optimize that in a much broader operation?
So the workforce is a critical part of what we’ve been focusing on, not only to attract new talent, but to train existing talent that has been in the company for quite some time. We train them and redeploy them where they need to be, and we’re doing that with our customers by creating an innovation center to help our customers understand AI-driven solutions and how they can bring their workforce along the journey.
A big part of what we’re talking about is change management, right? A change in the way we work.
When we started the COVID lockdowns, for example, it brought more people online and they started using Teams or Skype. Skype is now gone, rest in peace… But in order to communicate with families, we shifted the way we connect with people, and we need to do the exact same thing to help the workforce really understand the value of AI.
All the research that has been done so far indicates that the technology actually creates more jobs. It reduces some of the mundane work that people used to do on a regular basis and allows them to focus their human intelligence, which, when combined with artificial intelligence, can have a broader impact on the productivity of the enterprise and organization.
“Human intelligence is a critical component of what we see as closing the loop with AI. It can not be AI alone. It has to be complimented by human intelligence, because someone has to benefit from it, and it’s not by reducing the workforce. It’s actually by leveraging the workforce to do something better and more impactful.”
– Hany Fouda, senior vice president of Schneider Electric Process Automation
Paul: So does that change the type of person you’re looking to hire? I imagine it used to be imperative that a highly-trained engineer or mathematician come in and make sense of all this data, right? And it’s not like that now, necessarily, when you might want someone who is better at talking to machines. That seems like a different skill.
Hany: It is. And this is part of the adaptation and the change that we have to go through. I think there is room for everyone, but the skill set will definitely evolve. You will see, for example, a high demand for prompt engineers who are talking to the machines. This cycle will pass as well. There will be stabilization in the kind of skill set that we’re looking for. We have seen it with the personal computer and with the Internet. The Internet is becoming more adaptive to what consumers are looking for in terms of video sharing, music sharing, and so on. But in the early stages, you were hiring engineers who were mainly capable of HTML coding, right? And that changed dramatically over time. So there is no one size fits all, and there is always a space to retrain people and redeploy them, as we are doing in Schneider Electric.