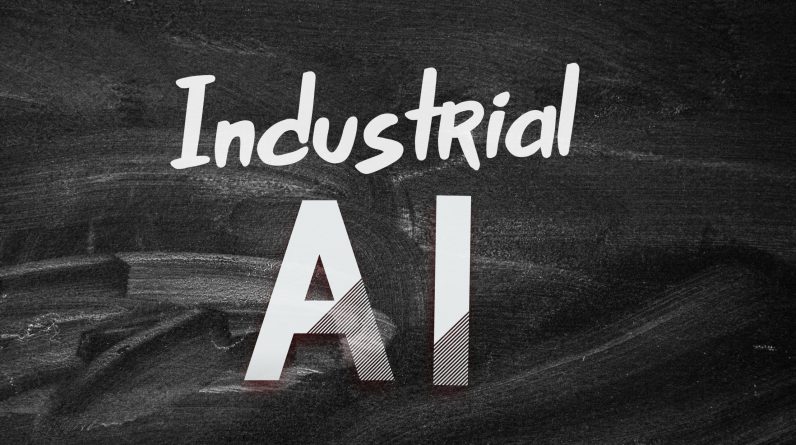
Enhanced quality control, elevated safety standards and customised training through RAG deployment can all drive improvements in operational efficiency, writes Łukasz Koczwara, CTO at IT consultancy STX Next
Koczwara – RAG will help Industry 4.0
With the AI boom already well underway, the vast majority of manufacturers have begun researching and implementing this technology in efforts to boost efficiency. However, AI adoption does not guarantee instant success, with a recent Deloitte survey revealing that 91% of AI projects in manufacturing fail to meet expectations, either in terms of benefits or time invested.
Manufacturers can achieve an AI strategy that exceeds expectations by adopting Retrieval Augmented Generation (RAG). This is a form of AI that is fully developed and ready for deployment, acting as a gateway to the wider integration of AI solutions.
Defining RAG
Retrieval Augmented Generation (RAG) is like a super-efficient assistant, instantly pulling up all the maintenance records, manuals and past issues of every machine under the care of a manufacturer. It then uses this information to identify when machines may need servicing or what parts a firm should order in anticipation of a breakdown.
This technology can even create diagnostic instructions for a defect that has never previously been documented, making it ideal for instances where data is highly complex and appears in different forms. Deploying RAG is not a classic rip-and-replace situation. Instead, it layers on top of existing IT systems and starts working on all use cases immediately.
Industry problem
In a report published by Hexagon earlier this year in collaboration with Forrester, an astounding 98% of manufacturers admitted to struggling with data and data-related issues. This highlights that, despite having vast quantities of extremely valuable information at their fingertips, manufacturers are unsure of how they can unlock the potential of this resource.
RAG can help manufacturers make the necessary transition from data-phobic to data-driven, transforming the information firms possess into a genuine asset that can streamline operations across the board. With so many manufacturers suffering from the same problem, it’s clear that taming this data and allowing for solutions such as RAG to be deployed is a clear route to establishing competitive advantage over rivals.
Consistent quality
A prime example of where RAG can have a positive impact is in quality control, where manufacturers compare previous control values with current values. Ensuring products are of consistently high quality is integral for all manufacturers: if customers are regularly receiving goods of varying standards, they will quickly lose trust in the brand and start to look elsewhere.
RAG systems can perform quality control in real time on a massive scale, detecting anomalies and predicting potential defects before products leave the factory floor. By retrieving and synthesising past inspection reports, specifications and standards, RAG tools are able to guide inspectors through complex quality checks. As a result, firms ensure high quality is maintained on a consistent basis, while reducing the volume of waste they produce.
Safer environment
Safety is another top priority in manufacturing, and the advent of RAG enhances the ability to assess risks with unprecedented precision. It is true that firms that do not put the correct precautions in place can face extreme repercussions if an accident occurs, but this shouldn’t be the defining element of a manufacturer’s approach to employee safety. It’s important that all organisations in the industry show genuine care for staff and take precautions wherever possible to ensure their security.
By sifting through safety reports, incident logs and compliance guidelines, RAG can alert management to areas of concern and help develop more effective safety protocols, minimising the likelihood of accidents. This includes comparing different procedures and providing evidence to explain why one procedure may be more effective than another.
Personalised training
Training new employees is a significant source of stress for manufacturers, typically taking up considerable time with firms putting little effort into tailoring tutorials to each individual. However, it’s still an element of everyday activity that should be treated very seriously, as firms who aren’t committed to providing insightful, engaging and helpful training schemes for both new and existing employees are likely to struggle to maintain staff morale and retain the best people.
Not only are inadequately trained employees less skilled at their jobs, but they also feel less motivated if they believe their employer isn’t investing in their future, with both instances leading to decreased productivity. Furthermore, the manufacturing industry is facing a well-documented skills crisis, with firms having to fight to attract and retain talent. Employees who aren’t growing in their role due to the inadequate provision of opportunities are sure to seek better options elsewhere.
To avoid these undesirable scenarios, manufacturers can transform their approach to training and development through the integration of RAG. This technology customises training materials based on job roles, current trends and individual learning progress, allowing firms to provide bespoke training at a fraction of the previous cost.
Predictive maintenance
In a capital-intensive sector such as manufacturing, it’s essential that firms consider ways they can keep machinery in peak condition, without spending huge amounts on stocking and storing replacement parts. The ultimate goal should be to pre-empt any breakdowns and be equipped to address the problem, which is only achievable with the support of technology.
For the last few years, the most advanced predictive maintenance detection systems have been based on earlier-generation AI. One of the benefits of RAG is that an even more powerful AI is applied to all systems, old and new. This of course means less downtime, lower maintenance costs and an overall boost in productivity.
Ready-made solution
RAG is not a distant, futuristic concept: it is a here-and-now solution with tangible benefits for manufacturers. By introducing RAG into existing operations, firms are not just adapting to the evolving landscape of Industry 4.0, they’re actively shaping it. From superior quality control to enhanced safety protocols, RAG stands to redefine the capabilities of modern manufacturing.