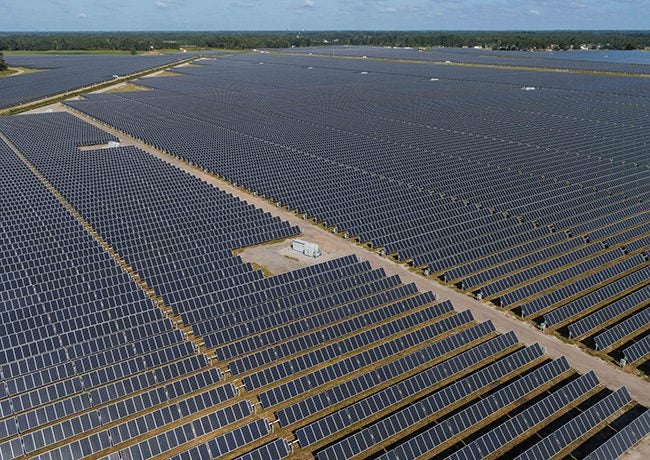
Photovoltaic (PV) systems eventually lose their ability to generate power, leaving asset owners with a major decision on what to do next. Whether it’s outright damage from extreme weather events or expected gradual degradation, equipment decline over time is inevitable. These considerations can help asset owners assess whether or not to repower, and then take steps to repower effectively if that’s the right course of action.
![]() |
1. A repowering project at a solar farm can include replacing modules, inverters, and related equipment. It also may involve adding energy storage to an existing array. Courtesy: DEPCOM Power |
Should I repower? In brief, repowering (Figure 1) involves replacing modules, inverters, and related equipment. Asset owners and operators can utilize a systemic decision-tree style process to answer this question.
Step one: What are the causes of degradation and/or power loss, and what’s our objective?
■ A Plant Is Underperforming. As modules age and they reach an expected end of life, or when premature failures contribute to module and/or inverter underperformance, the distressed assets need to be replaced to return a plant to original production and peak performance.
■ Catastrophic Events. Damage from natural disasters can prompt a sudden need for site repowering, but the decision is not as simple as it seems. Off-the-shelf components may no longer be manufactured or available. Replacing modules could require full redesign and reengineering.
■ Business Changes Require Action, with or without Power Loss. Project financials change as power purchase agreements (PPAs), Solar Renewable Energy Certificates (SRECs), and other contracts near the end of the original term. Repowering and adding energy storage can bring continued and additional value to your asset.
Step two: What financial recovery is available?
■ Insurance Availability. Determining whether or not damage and asset losses are covered as an insurable loss is a big part of a repowering decision and strategy.
■ Warranty Availability. Is the equipment still under warranty and supported by the original manufacturer? If so, asset owners may be able to get new life out of a PV system. For example, back-sheet delamination may be the underlying cause of power loss and a valid warranty claim.
■ Avoided Costs/Losses. Repowering and restoration may provide a positive return on investment (ROI) by preventing repair costs, energy loss, and associated damages. Adding additional PV capacity and/or energy storage may further contribute to the ROI.
Step three: Is there a business case?
■ PPA Status. To comply with a PPA, sites need to produce at the levels stated in the contract. When parts reach a certain age or components stop working, it may be an asset owner’s responsibility to repower and return the site to full production. What’s more, if a PPA expires, the terms of a new agreement may not be as attractive as the original contract.
■ Tax Equity. Repowering doesn’t necessarily provide tax equity, which leaves owners with the question of how to finance underproduction when not covered by insurance or warranty. If liquid funds are not available, it could potentially be less expensive and more financially feasible to decommission a site.
Step four: Repower or decommission?
By answering the first three questions, an asset owner or operator has the information needed to make a strategic decision. If there is not enough financial recovery or a strong enough business case to justify repowering, then decommissioning is a viable choice. If repowering is the most suitable path forward, a new structured process begins to return a plant to full power.
Restoring a Plant After Inverter Fire Damage—Roadmap for Repowering
Once an owner has given the go-ahead to repower a plant, the baton is passed to the operations and maintenance team or a partner specialized in PV plant repowering. This could include repairing damaged equipment (Figure 2), in addition to upgrading existing assets.
![]() |
2. DEPCOM Power helped restore this solar power facility after an inverter fire damaged equipment. Courtesy: DEPCOM Power |
Step one: Detail the technical and business case.
Technical Case. One of the project team’s first responsibilities is generating a benchmark understanding of the condition of the site for the asset owner. Benchmarking includes detailed technical assessments and specifications, such as:
■ A system review that considers currency of design, such as whether or not components are outdated, and if they simply need to be replaced or if a full re-engineering is warranted.
■ An outline of technical aspects of repowering, including a process of matching equipment to inverters, determining if module racking is reusable, and tallying up all necessary replacements.
■ A preliminary project schedule, based on general equipment lead time and key milestones, that prioritizes recovery and uptime.
Business Case. The business case is a strategic approach to repowering that goes beyond the equipment and technical case, including the following actions and considerations:
■ The asset owner weighed the PPA, ownership horizon, and availability of capital and incentives when deciding to repower, and now a service provider includes the details of each in a complete plan.
■ With regulatory limitations and restrictions varying from year to year, there could be new macro environment factors to integrate into a repowering approach. For example, restrictions may limit an owner’s ability to upsize, and mandate that a new design will need to match the original design as much as possible.
■ A standard cost/benefit analysis to determine the best use of capital, such as repair vs. full replacement, rounds out the business case.
Step two: Complete a detailed site visit.
In step two, the strategy is set and the tactical work kicks in. Engineering and construction experts armed with tape measures and cameras verify dimensions, locations, and specifications. Engineering, procurement, and construction expertise and resources are not just “nice to haves” in a repowering project, they are necessary to gain a full understanding of any proposed solution’s feasibility.
![]() |
3. A repowering project may include repairs to a solar farm’s equipment, in this case, after a severe wind event damaged trackers and modules. Courtesy: DEPCOM Power |
Safety is paramount to a site visit. In particular, sites with extreme weather damage (Figure 3) will require a custom safety protocol before any on-site work can begin. For example, visitors to a heavily damaged site will need to prepare for abnormal conditions, including broken glass, sharp edges, flooded conditions, and live wires or electrical issues. In brief, a detailed site visit follows three primary steps:
■ Safety orientation and verification accounting for an array of abnormal conditions. It’s critical that a qualified company provides this verification.
■ Photo documentation of affected equipment, damage, and primary interface points between new and existing equipment.
■ Aerial inspection for any scope of work involving a large number of modules, inaccessible areas, or other suspected damage.
Step three: Develop a new project design.
It’s atypical that a repowering project will entail a simple equipment swap in a finite area of a site. It’s more likely that a project will require a minor or full redesign. Evolution of the PV industry and its equipment happens at a relatively rapid pace. For example, code changes in 2014 resulted in new 1,000-Vdc equipment replacing 600-Vdc equipment. In 2017, code changes allowed 1,500-Vdc equipment in utility-scale systems. While this change directly reduced system costs, it effectively rendered 600-Vdc and 1,000-Vdc equipment obsolete for this application.
Advanced technology helps move the industry forward, but it also means that new equipment is not always backward compatible. A component may need to be replaced not because it’s degraded, but because it’s no longer compatible with the companion equipment that needs to be upgraded. Central inverters are particularly challenging to match to an existing array and alternating current (AC) collection system, and string inverters may present a more cost-effective solution in some cases.
Replacing perfectly good inverters and transformers because they no longer fit with the rest of the repowering effort can hike costs by tens of thousands of dollars. Creative engineering solutions that thoughtfully blend older units with state-of-the-art technologies can prevent this cost escalation.
Step four: Assign a budget and schedule.
Every asset owner has different ROI criteria, in part because the more recent phase of solar industry growth is in its early stages. Creating and adhering to a budget, project plan, and schedule will ensure that a repowering effort is successful and worth the effort (see sidebar).
Case Study Snapshot This case study details repowering for a 70-MW plant with an operations and maintenance contract, and a 10- to 15-year ownership horizon. The challenge: Inverters cost the owners significantly more to operate than expected due to premature failures. The solution: The owner followed the “repower or not to repower” decision process and examined whether to fully decommission the site and return it back to seed, replace all inverters in a phased approach, or replace all inverters at once. The owner determined that energy storage could provide additional financial advantages, and new incentives and federal programs made repowering with batteries more attractive. The takeaway: The most effective and efficient decision could involve a mix of creative strategies that consider the long-term value and not just immediate repairs needed. |
One of the biggest questions an asset owner or operator will ask is: “Will I have to do this again in a few years?” This question circles back to the original decision process, and underscores the importance of viewing a project with a focus on the long-term, and not approaching a repowering project as a mere repair job. Ultimately, repowering based on an organized decision process is a form of future-proofing a plant, protecting an owner’s investment, and maximizing power availability for all stakeholders.
—Ananda Hartzell is vice president of business development for repowering services at DEPCOM Power, a Koch Engineered Solutions company. He has more than 20 years of experience in the PV industry in all aspects of engineering, product management, and technical sales.